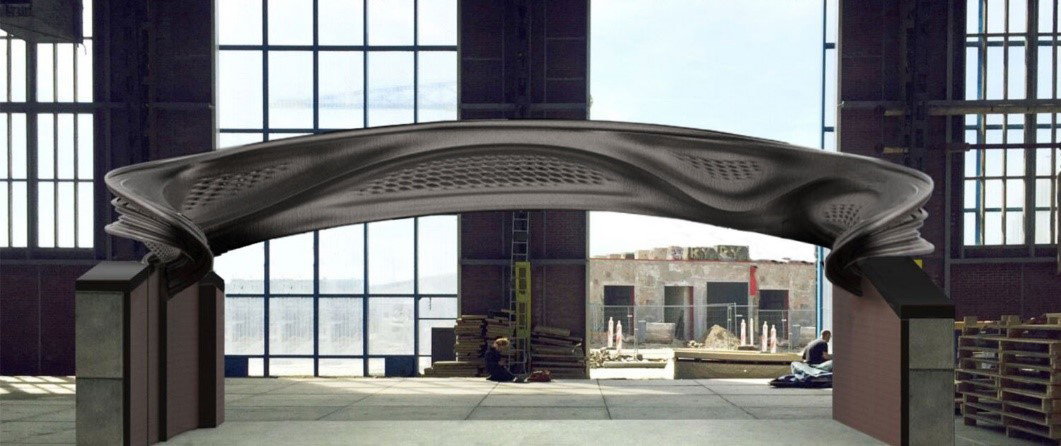
Comparison and modelling of fatigue strength of 3D printed 308 stainless steel and parent metal
Wire and arc additive manufacturing (WAAM) has proven that it can produce medium to large components because of its high-rate deposition. To improve the usability of WAAM the material properties must be known and the process must be optimized to lower the cost of production.
Introduction
Wire and arc additive manufacturing (WAAM) has proven that it can produce medium to large components because of its high-rate deposition. To improve the usability of WAAM the material properties must be known and the process must be optimized to lower the cost of production. In addition to the monotonic strength properties, the fatigue strength of safety-relevant components is crucial for the applications in which the material is cyclically loaded. Porosity is a typical defect in AM processing that needs to be minimized due to adverse effects on mechanical properties. Porosity determines a lower static strength and a lower fatigue strength due to the reduced crack initiation time. In terms of modelling of defects and fatigue life prediction, there are three approaches in the literature, namely, statistical, classic notch fatigue method treating porosity as a stress raiser, and fracture mechanics approach. However, parts made of wire-based AM processes exhibit far fewer and isolated pores, hence the use of the statistical approach may not be suitable.
Goal
The graduation project has the following aims:
• Comparison of chemo-mechanical properties of AM specimens of 308 stainless steel and specimens of parent metal (chemical composition, tensile properties, toughness, hardness);
• Characterizing the fatigue strength under constant amplitude of AM specimens machined from blocks of 308 stainless steel, in the parallel, perpendicular and 45 degrees angles with respect to the direction of printing, and compare it with specimens machined from parent metal;
• Identify the defects causing fatigue failure and their source (nucleated defects induced by fatigue or intrinsic defects caused by the manufacturing process), and model their effect into a fracture mechanics framework, e.g. (Murakami, 2021), using FEM or analytical models (Skallerud, 1993), (Nourian-Avval, 2020), (Hidalgo, 2019) .
Assumptions
The blocks will be provided by MX3D and are produced with best suited and known process inputs (printing speed, heat input, etc.) selected by MX3D. The fatigue tests will be executed under CA loading in the high cycle fatigue regime and up to a significant number of cycles. The tests will be executed using a rotating bending machine.
Supervision
The graduation project will be supervised by Dr. Davide Leonetti and Prof. Bert Snijder from TU/e-SED, and Ir. Jean-François Moulin from MX3D. The starting date is expected in mid-late November 2021, or December. The graduation project is a pilot financed by the BOOST! Program, and supported by MX3D.
References
Murakami, Y., Takagi, T., Wada, K., & Matsunaga, H. (2021). Essential structure of SN curve: Prediction of fatigue life and fatigue limit of defective materials and nature of scatter. International Journal of Fatigue, 146, 106138.
Skallerud, B., Iveland, T., & Härkegård, G. (1993). Fatigue life assessment of aluminum alloys with casting defects. Engineering Fracture Mechanics, 44(6), 857-874.
Nourian-Avval, A., & Fatemi, A. (2020). Fatigue life prediction of cast aluminum alloy based on porosity characteristics. Theoretical and Applied Fracture Mechanics, 109, 102774.
Hidalgo, R., Esnaola, J. A., Llavori, I., Larrañaga, M., Hurtado, I., & Herrero-Dorca, N. (2019). Fatigue life estimation of cast aluminium alloys considering the effect of porosity on initiation and propagation phases. International Journal of Fatigue, 125, 468-478.