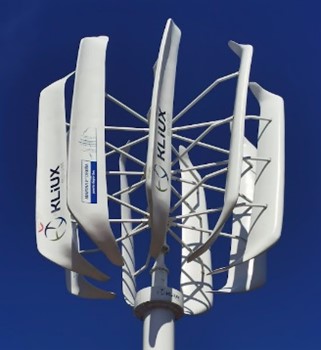
Dynamical Response of Cold-Formed Steel Structures to the Action of New
This project aims to optimize PowerNEST, a renewable energy system combining solar panels and wind turbines, by using lighter cold-formed steel in its structure. The research will focus on predicting the dynamic loads from vertical axis wind turbines and assessing the structural performance through simulations to ensure safety and durability.
Introduction
The real estate industry is under great pressure. Companies have to comply with strict laws and regulations from governments and goals from other parties to make their properties more sustainable. PowerNEST – a solar and wind energy-generation construction on top of a building, may be part of the solution, Figure 1 on the left. It is, briefly explained, a nest of solar panels that contains a wind turbine, and for which multiple of these modules can be placed on a roof. The system can utilise more than 100% of the normal roof area; the wind is captured and accelerated by the Venturi effect; solar panels are air-cooled; and two-sided solar panels and reflective surfaces yield more solar energy. To improve the system further, a new design is proposed, which seeks to replace as much as possible hot-rolled steel sections with cold-formed steel, Figure 1 on the right. This lowers the amount of material used, but also widens the number of applications, for the system becomes significantly lighter. However, it is yet unknown how such a cold-formed structure responds to the actions of the (new design) vertical axis wind turbines, with respect to e.g. deformations, strength, vibrations, and fatigue.
Figure 1, left: PowerNEST with a vertical axis wind turbine, middle: new turbine design, right: part of the proposed cold-formed steel structure, with the wind turbine mounting point in the middle.
Research goals
To ensure the safe application of vertical axis wind turbines within cold-formed steel structures, research goals are (a) a strategy for the prediction of the dynamical loads of the wind turbine on the structure, based on experimental data, theoretical models, or simulations, and the translation of these into a useful format to assess the structure; (b) the development of a finite element model to simulate all relevant parts of the structure by the finite element method, such that its dynamical response can be researched; (c) a list of relevant response characteristics checked against design requirements, such as the limitation of displacements, possibly related to resonances; maximum stresses; and fatigue criteria.
Method
The project will start with a thorough study of research already carried out on the mechanical actions of vertical wind turbines, finite element models for structures under dynamic loads, and cold-formed steel structure fatigue problems. Furthermore, the basics of dynamics should be studied. Based on the findings, a strategy is developed for the prediction of the dynamical loads of the wind turbine on the structure. Probably experimental data will be used, or results for existing simulations, and these are transformed in either a time-domain or frequency-domain loading scheme. Secondly, a finite element model is developed to simulate all relevant parts of the structure by the finite element method, such that its dynamical response can be researched. Either implicit or explicit time-domain analyses are carried out, or frequency-domain simulations, partly based on modal analysis. Finally, a list of relevant response characteristics is composed, in cooperation with industry, to be checked against design requirements. For instance, relevant may be the limitation of displacements, possibly related to resonances, maximum stresses, and fatigue criteria.
Requirements
We are looking for an enthusiastic and bright student, interested in dynamics, the finite element method, (steel) structures, engineering, and sustainability, with good to high grades for the Applied Mechanics courses. A rewarding and state-of-the-art project is offered, in combination with industry (IBIS Power and CFP Engineering). The project will be supervised by Dr. Hèrm Hofmeyer (SED), a second TU/e professor, and staff of IBIS Power and CFP Engineering.